富士石油の大きな強みの一つが「安全確保、安定操業への取り組み」と言えます。1968年の袖ケ浦製油所の操業開始以来、「安全の確保」は富士石油にとって基本理念の一つであると同時に、会社のビジョンでも「安全を第一優先」と謳っております。
安全確保、安定操業への取り組みは、設備やシステムの対応も重要ですが、それだけでは不十分です。それらを十分に活かせる「人財」がいなければ「宝の持ち腐れ」に過ぎません。従って、袖ケ浦製油所の安全確保、安定操業への取り組みは、ハード面(設備・システム)とソフト面(人財)を両輪として推進されています。ちょっと専門的になりますが、ここでは、その取り組みをご紹介しましょう。
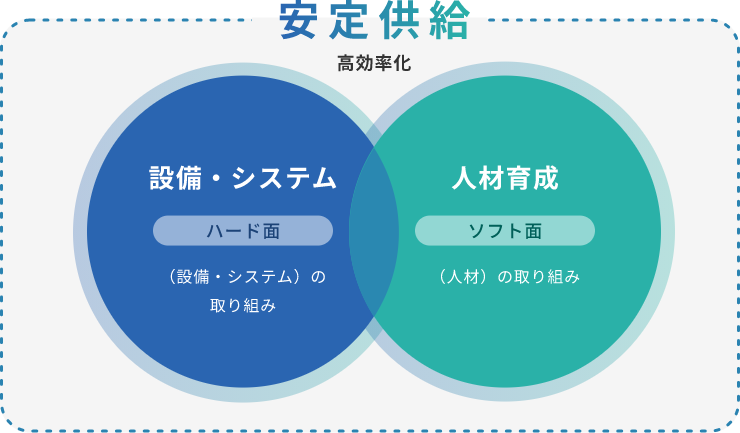
計器室統合の有効性
袖ケ浦製油所では、2009年に、それまで4ヶ所に分散していた計器室を1ヶ所に統合し、併せて操業制御システムも統合しました。これにより、情報の一元化・共有化、スピーディな情報伝達が可能となったことで製造部門全体での協力体制が確立され、効率化と安全・安定操業体制の強化が図られています。
2011年3月11日の東日本大震災では、計器室が1ヶ所に集中していたことにより、地震直後の点検・運転変動への対応など、的確かつ迅速に実行。その結果、事故・トラブルを起こすことなく、ほぼフル稼働を維持継続することができました。
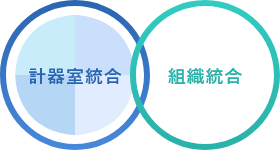
緊急脱圧システムの導入
大地震などの緊急時には製油所内の複数の装置を緊急停止させる場合がありますが、各装置の内部には大量の可燃性ガスが存在します。この可燃性ガスを安全に排出しながら迅速に装置を停止させるためには高度な制御システムが必要です。袖ケ浦製油所ではいち早く国際的な安全規格に適合した安全ロジックに基づく電子制御システムを個別装置の緊急停止プログラムや大規模地震発生時に自動的に行われる全装置緊急停止・脱圧システムに採用しました。
これにより大地震のような万一の場合でも安全かつ自動的にすべての装置を停止することが可能です。
重要なケーブルの二重化
製油所内には動力ケーブルや通信ケーブルなど様々なケーブルが人間の神経のように張り巡らされています。その中で特に重要なケーブルが、統合計器室に直接繋がるLANケーブル群です。袖ケ浦製油所では、これらのケーブル群を二重化し、しかも異なるルートで統合計器室に繋がっています。
これにより、災害等でケーブルが遮断されても、別のルートのケーブルがバックアップすることで安定した操業を維持することができます。
4.訓練シミュレータの導入
従前は毎年、全ての装置を停止して行っていた定期修理も、最近では4年連続運転が可能となりました。プラントは、飛行機と同じで離陸するときと着陸するとき、即ち、装置を動かすとき(スタートアップ)と停止するとき(シャットダウン)が最もリスクが高くなります。従って、これらの経験が少なくなることは、逆に緊急時のリスクが高まることも意味します。
このため、袖ケ浦製油所では「ダイナミック訓練シミュレータ」を導入し、航空機の訓練用シミュレータと同様、実際に装置を運転する感覚で訓練を行っています。スタートアップやシャットダウンは勿論、トラブル時の対応についても常に準備を万全にしているのです。
組織の統合の有望性
2009年の計器室・制御システムの統合に伴い、袖ケ浦製油所では、製造部門の6つの課を3つに統合しました。これにより1グループの人数が増えることになり、緊急時のトラブル対応力が増しています。また、技術伝承をスムースに行うためにも有益であり、計器室の統合とも合わせ、シンプルな組織とすることにより、情報の迅速な共有化・伝達も可能となっています。(先に述べたように、これは東日本大震災の時に大きな威力を発揮しました。)
しかし、各グループが担当するエリアも担当する装置もほぼ2倍になったため、オペレーターにとっては大変です。新たに担当する装置のことも覚えなければならず、2009年の課統合以降、4年間にわたる教育計画を立案し、今日まで実施してきています。
現在では、製油所を広範囲で理解するオペレーターとなり、安全確保、安定運転に大きく寄与するとともに、効率運転にも貢献しています。
「オペレーター」から
「オペレーション・エンジニア」へ
オペレーター(運転員)は、単に装置を運転するだけではありません。「自ら考え、自らより良い方法を提案できる」エンジニアを目指しています。
「安全確保、安定運転に重要な役割を果たす」、これはまさに「オペレーター」ではなく「オペレーション・エンジニア」の姿なのです。
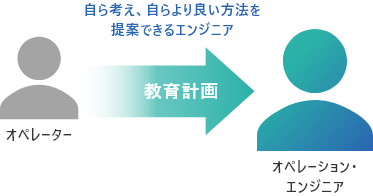
外面腐食総点検による安全確保
配管の腐食開口による漏洩は、危険物を扱う製油所では重大な問題です。勿論、保全部門は万全の態勢で配管の検査を行っていますが、製油所内の配管の長さは膨大であり、全てを網羅することはできません。
オペレーション・エンジニアたちは、保全部門と共同で作成した「外面腐食の起きやすい構造図」を用い、計画的に外面腐食総点検を自発的に実施しています。そしてこれが外面腐食の早期発見につながり、安全の確保、安定運転に大きな役割を果たしています。
人は財産
これまで製造部門の取り組みを中心にご紹介してきましたが、製造部門を支える保全部門、安全・環境部門、管理部門も、安全の確保、安定運転に大いに貢献しています。月に1回、製油所全部門総動員で設備の点検や製造現場の清掃をする「パワープレイ総点検」などはその好例と言えるでしょう。その他にも「ヒヤリ・ハット活動」「危険予知活動」「無事故・無災害キャンペーン」「防災訓練」など、全所員を挙げて安全確保、安定運転に取り組んでいます。まさに、富士石油では「人は財産」なのです。
富士石油では、さらなる競争力強化・効率化に向けて「世界水準の生産技術」を目指しています。これもハード面とソフト面の両面からアプローチしています。
- 拡大
- 計器室統合化と安全・安心運転へ向けた取り組み
原油ブレンドシステムの導入
製油所で処理する原油の種類は多岐にわたります。処理原油の油種が変わると、それに適した運転に調整する時間が必要となるため、その分ロスが発生します。
袖ケ浦製油所では、複数タンクの原油をブレンドできるシステムを構築しており、処理する原油の性状を調整することによって運転の変動を抑制しつつ安定運転を可能としています。
中間タンクの削減
製油所では様々な装置を通して石油製品を製造するため、中間製品(半製品)も多く、これらを貯蔵するタンクも数多く存在します。
袖ケ浦製油所では、原油ブレンドシステムを始め高度制御システムの導入などにより、生産から出荷まで一貫してロスを削減する体制を構築。中間タンクを削減しています。
また、ロスの削減のみならず、余剰となった中間タンクを輸出用タンクに転用するなど戦略性を高めることも目指しています。
統合計器室
計器室の統合は、情報の集中化・共有化、製造部門全体での協力体制の確立を促進し、操業の効率化にも大きく寄与しています。
生産計画系の高度化
製油所の効率性を追求するためには、生産計画系の高度化は欠かせません。このため実際の操業データを常にフィードバックし、生産計画システムの精度の向上を図っています。
これにより、計算計画値と運転実績値の誤差を最小限にとどめ、製油所の効率操業を実現しています。
高度制御システムの導入の効果
製油所では、処理原油の油種の変更や生産する石油製品の種類の変更などの際、運転変更が必要となりますが、その運転調整のための時間と、これに伴うロスが発生します。このため、装置ごとに高度制御システムを導入し運転調整時間の短縮を図り、ロスの削減とともに中間タンクの削減にも繋げています。
情報の共有化
富士石油では、XHQと呼ばれる「操業情報共有化システム」を導入しています。これにより、製油所のみならず、本社においても詳細な操業情報がリアルタイムで把握できるとともに、緊急時のみならず、問題が発生した際も迅速に情報の共有化が可能となっています。
2011年3月11日の東日本大震災では石油施設も大きな被害を受け、東北・関東の製油所9か所の内、6か所で操業が停止しました。しかしながら、石油業界は会社の枠を超えた一丸となった取り組みにより、概ね3週間で震災前の供給体制に戻すことができました。他のライフラインの復旧に相当の時間を要したことを考えると、基幹エネルギーとしての石油の利便性・有用性が示されたものと言えます。
富士石油袖ケ浦製油所では、多くの製油所が停止した東日本大震災においてもフル稼働を維持し、震災発生翌日の早朝から出荷を再開し安定供給責任を果たしてまいりました。この背景には、富士石油の社員が一丸となって進めてきた「安全確保・安定操業」への取り組みがあったことは勿論ですが、アラビア石油の開拓・チャレンジ精神やわが国のエネルギーを支え続けた精神などが一人一人のモチベーションを支える底流にあったことも事実です。そして、こうした社員一人一人の高いモチベーションこそが、安定供給・競争力強化・安定成長を支える基盤でもあります。
わが国のエネルギーを巡る環境は大きく変化しつつありますが、一次エネルギー供給に占める石油の割合は未だ第1位の座を占めており、今後も石油が基幹エネルギーであり続けることが予想されます。
このような状況の下、富士石油は、基幹エネルギー供給を担う企業として、安全・安定運転を継続することにより、競争力の強化にも努めて参ります。これからは、国内に加え海外のマーケットも対象として安定的かつ積極的な収益を追求し、企業価値の最大化を図って参ります。