Another key strength of Fuji Oil is its initiatives to ensure safe and stable operations.
Since the Sodegaura Refinery came on stream in 1968, ensuring safety has been one of our fundamental principles. Our corporate vision also emphasizes “safety first.”
Safety initiatives that target facilities and systems are important, but these efforts are insufficient on their own. Without skilled personnel assets* to make full use of these improvements, cutting-edge facilities are meaningless.
To ensure safe and reliable operations at our Sodegaura Refinery, we therefore implement initiatives at an infrastructure level (facilities and systems) and at a personnel level. In this section, we look in more detail at some of these safety initiatives.
* We refer to our human resources as an asset, because we believe our workforce is one of our most important resources.
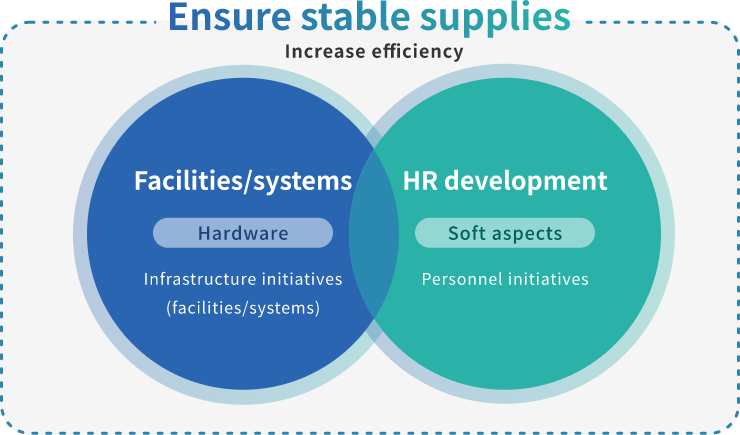
The effectiveness of control room integration
In 2009, the Sodegaura Refinery consolidated its four separate instrument rooms into one location, and also consolidated its operational control systems. This enabled the centralization, sharing and speedy transmission of information, establishing a system of cooperation across the entire manufacturing department and strengthening efficiency and the safe and stable operation system.
During the Great East Japan Earthquake on March 11, 2011, the fact that the control rooms were all concentrated in one place enabled us to carry out inspections immediately after the earthquake and respond to operational fluctuations accurately and swiftly. As a result, we were able to maintain almost full operation without any accidents or problems.
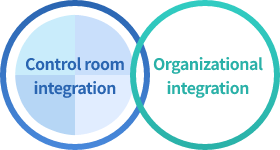
Introduction of emergency decompression system
In the event of an emergency such as a major earthquake, multiple pieces of equipment in a refinery may need to be shut down, but each piece of equipment contains large amounts of flammable gas. An advanced control system is required to shut down the equipment quickly while safely discharging this flammable gas. The Sodegaura Refinery was one of the first to adopt an electronic control system based on safety logic that complies with international safety standards for the emergency shutdown program for individual equipment and the emergency shutdown and depressurization system for all equipment, which is performed automatically in the event of a major earthquake.
This makes it possible to safely and automatically shut down all equipment in the unlikely event of a major earthquake.
Important cable redundancy
A variety of cables, including power cables and communication cables, are spread throughout the refinery like human nerves. Among these, the most important cables are the LAN cables that connect directly to the integrated control room. At the Sodegaura Refinery, these cables are duplicated, and are connected to the integrated control room via different routes. This means that even if a cable is cut off due to a disaster, another cable route will back it up, allowing stable operations to be maintained.
4. Introduction of training simulators
Previously, all equipment was shut down every year for scheduled maintenance, but recently, it has become possible to operate the plant for four consecutive years. Like an airplane, the highest risks for a plant are when it takes off and lands, that is, when the equipment is operating (startup) and when it is stopped (shutdown). Therefore, less experience in these situations also means that the risk of an emergency increases.
For this reason, the Sodegaura Refinery has introduced a "dynamic training simulator," and, like aircraft training simulators, training is conducted with the feeling of actually operating the equipment. The refinery is always fully prepared not only for startups and shutdowns, but also for dealing with problems.
Promise of organizational integration
With the integration of the control room and control system in 2009, the Sodegaura Refinery integrated six sections in the manufacturing department into three. This increased the number of people in each group, improving their ability to respond to emergency problems. It is also beneficial for smooth technology transfer, and by simplifying the organization, combined with the integration of the control room, it is possible to quickly share and transmit information. (As mentioned earlier, this proved to be a great help during the Great East Japan Earthquake.) However, the number of areas and devices each group is responsible for has almost doubled, which is difficult for operators. They also have to learn the new devices they are responsible for, so since the integration of the sections in 2009, a four-year training plan has been drawn up and has been implemented to this day.
Now, as an operator with a comprehensive understanding of the refinery, he is making a significant contribution to ensuring safety and stable operation, as well as efficient operation.
From "Operator" to "Operation Engineer"
Operators do more than simply operate equipment. They aim to be engineers who can "think for themselves and propose better methods."
"Playing an important role in ensuring safety and stable operation" - this is exactly what an "operation engineer" is, not just an "operator."
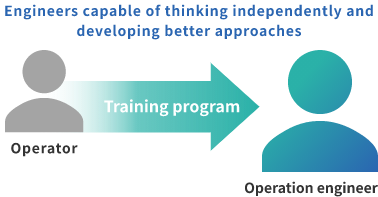
Ensuring safety through comprehensive inspection of exterior corrosion
Leaks due to corroded openings in pipes are a serious problem in refineries that handle hazardous materials. Of course, the maintenance department inspects the pipes in a thorough manner, but the length of pipes in the refinery is enormous, and it is not possible to cover them all.
Operation engineers use a "structural diagram showing where external corrosion is likely to occur" created jointly with the maintenance department to voluntarily carry out comprehensive inspections of external corrosion in a planned manner. This leads to early detection of external corrosion, playing a major role in ensuring safety and stable operation.
People are assets
So far we have focused on the efforts of the manufacturing department, but the maintenance, safety and environment, and management departments that support the manufacturing department also make a great contribution to ensuring safety and stable operations. A good example of this is the "power play general inspection" that takes place once a month, when all refinery departments are mobilized to inspect equipment and clean the manufacturing site. In addition, all staff members work together to ensure safety and stable operations through other activities such as "near miss activities," "risk prediction activities," "campaigns for zero accidents and zero disasters," and "disaster prevention training." Indeed, at Fuji Oil, "people are assets."
Fuji Oil is aiming to achieve "world-class production technology" to further strengthen its competitiveness and improve efficiency. This is also being approached from both the hardware and software sides.
- 拡大
- Initiatives for control room integration and safe, secure operation
Introduction of a crude oil blending system
A wide variety of crude oil is processed at refineries. When the type of crude oil being processed changes, time is required to adjust operations accordingly, resulting in losses.
At the Sodegaura Refinery, a system has been built that can blend crude oil from multiple tanks, and by adjusting the properties of the crude oil being processed, this enables stable operation while suppressing fluctuations in operation.
Reduction of intermediate tanks
Because refineries manufacture petroleum products through a variety of equipment, they also produce many intermediate products (semi-finished products) and there are many tanks to store these.
At the Sodegaura Refinery, we have established a system to consistently reduce losses from production to shipping by introducing advanced control systems, including a crude oil blending system, and have reduced the number of intermediate tanks.
In addition to reducing losses, we also aim to increase our strategic value by converting surplus intermediate tanks into export tanks.
Integrated control room
The integration of the control rooms has promoted the centralization and sharing of information and the establishment of a cooperative system across the entire manufacturing division, greatly contributing to improved operational efficiency.
Advancement of production planning systems
In order to pursue efficiency at refineries, it is essential to improve the sophistication of production planning systems. For this reason, actual operational data is constantly fed back to improve the accuracy of the production planning system.
This minimizes the error between calculated planned values and actual operating results, realizing efficient operation of refineries.
Benefits of introducing advanced control systems
In refineries, when changing the type of crude oil being processed or the type of petroleum products being produced, it is necessary to change operations, but this requires time to make adjustments and generates losses. For this reason, we have introduced advanced control systems for each piece of equipment to shorten the time it takes to make adjustments, which not only reduces losses but also reduces the number of intermediate tanks.
Information Sharing
Fuji Oil has introduced an "operational information sharing system" called XHQ. This allows detailed operational information to be grasped in real time not only at refineries but also at headquarters, and enables information to be shared quickly not only in emergencies but also when problems occur.
Oil facilities were also heavily damaged in the Great East Japan Earthquake on March 11, 2011, and operations were halted at six of the nine refineries in the Tohoku and Kanto regions. However, thanks to a unified effort that went beyond company boundaries, the oil industry was able to restore the supply system to pre-earthquake levels in about three weeks. Considering that it took a considerable amount of time to restore other lifelines, this demonstrates the convenience and usefulness of oil as a core energy source.
Fuji Oil's Sodegaura Refinery maintained full operation even during the Great East Japan Earthquake, when many refineries were halted, and resumed shipments early in the morning the day after the earthquake, fulfilling its responsibility to ensure stable supply. Of course, the background to this was the efforts of Fuji Oil's employees as a team to ensure safety and stable operation, but it is also true that the pioneering and challenging spirit of Arabian Oil and the spirit that has continued to support Japan's energy were the underlying motivation that supported each employee's motivation. And it is this high motivation of each employee that is the foundation that supports stable supply, strengthened competitiveness, and stable growth.
Japan's energy environment is undergoing major changes, but oil still accounts for the largest proportion of primary energy supply, and it is expected that oil will continue to be the main energy source in the future.
Under these circumstances, Fuji Oil, as a company responsible for supplying the main energy, will strive to strengthen its competitiveness by continuing safe and stable operations. Going forward, we will pursue stable and proactive profits in both domestic and overseas markets, and strive to maximize our corporate value.