Since beginning operations at the Sodegaura Refinery in 1968, Fuji Oil Company, Ltd., has striven to elevate the company as a whole, while following a fundamental principle of "ensuring safety and protecting the environment."
Environmental Management System
Fuji Oil Company, Ltd. (FOC) has established the Environmental Management System at the Sodegaura Refinery, for which FOC obtained ISO14001 certification, and has been continuously and systematically undertaking improvement of the environment. Also, FOC is making eco-friendly products and extending considerations to energy-saving, prevention of air and water pollution and reduction of waste materials. This system is continuously reviewed and improved.
Supply of Eco-friendly Products
FOC is supplying such eco-friendly petroleum products to minimize the environment impact while satisfying the specifications required by customers. Having made necessary modifications to the production facilities, FOC has already started, ahead of the regulations, delivery of "sulfur-free" (max. 10 ppm) fuel products such as gasoline and gas oil in order to reduce SOx, NOx and PM.
Reducing output of heavy fuel, increasing production of gasoline
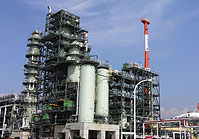
Gasoline: content of sulfur, etc. |
|
2000 |
Benzene: Max 1% |
2002 |
Premium Gasoline Sulfur: Max 10 ppm |
2005 |
Regular Gasoline Sulfur: Max 10 ppm |
2010 |
Supplying bio-gasoline |
To remove sulfur from gas oil for reduction of SOx, NOx and PM
Gas Oil: content of sulfur |
|
1997 |
Max 500 ppm |
2003 |
Max 50 ppm |
2005 |
Max 10 ppm |
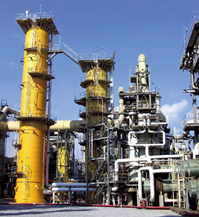
To produce low sulfur fuel oil and petroleum pitch by thermal-cracking of vacuum residue (asphalt fraction)
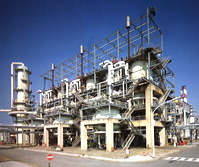
Low Sulfur Fuel Oil (High Pour Point) |
Low sulfur fuel oil (Sulfur Max 0.1%) is supplied to prevent air pollution. |
Petroleum pitch |
Heavy oil (asphalt) is converted to low-sulfur fuel through cracking. Petroleum pitch is also produced. Petroleum pitch is used as a boiler fuel and as a feedstock for coke used in the steel industry. |
Minimization of Environmental Impact
As part of wider efforts to protect the environment, the Sodegaura Refinery is implementing ongoing initiatives to reduce the environmental impact of its business operations.
Prevention of Air Pollution |
Severe restriction on emissions of SOx , NOx , etc. |
Prevention of Water Pollution and Conservation of Water Resources |
Purification of waste water with various water treatment facilities and recycling of industrial-use water. |
Control of Chemical Substances |
Adequate management of specified chemical substances, production of hazardous chemicals like benzene in sealed-structured facilities and the reduction in emissions of volatile organic compounds by stocking them in a storage tanks with its roof floating inside the tank. |
Reduction and Recycling of Waste Material |
A large reduction of waste materials by 94% in fiscal 2010 compared with the fiscal 1990 level (more than 95% of the target is already achieved) and thoroughgoing recycling and reuse of resources. |
Prevention of Oil Seepage in the Ocean |
Installation of detector and tank dike against oil spill, procurement of oil spill response equipment and frequent participation in training. |
Low-temperature Waste Heat Utilize System
Fuji Oil Company, Ltd. (FOC) has been stepping up its energy conservation efforts. At its Sodegaura Refinery, FOC has expanded the scope of energy conservation activities to include other plants operating in the same petrochemical complex. FOC has been working on a technology that utilizes low-grade waste heat with temperatures of 150ºC or lower. Until recently the waste heat had been merely released into the atmosphere due to the lack of alternative options. The new technology has been implemented in phases at the Sodegaura Refinery and adjacent Sumitomo Chemical Chiba Works. It has already conserved huge amounts of energy by harnessing the surplus low-grade waste heat to generate electricity.
FOC received the 2006 Agency for Natural Resources and Energy Director-General's Award from the Japan Machinery Federation jointly with Sumitomo Chemical Co., Ltd., and Chiyoda Corporation for its proven energy-saving initiatives.
The multiplant low-exergy utilize system consists of the following two subsystems.
The multiplant energy sharing system is designed to recover waste heat generated from multiple plants for joint use of energy. The low-temperature waste heat that is released from FOC's processing plant at temperatures between 80ºC to 150ºC is used to heat water piped in from the adjacent Sumitomo Chemical plant's boiler to a temperature of 110ºC via a heat exchanger. The heated water is then supplied back to Sumitomo Chemical, saving the boiler fuel normally used for heating.
The system utilizes waste heat that had been previously released into the atmosphere or cooling water to now heat boiler water and save energy as the result.
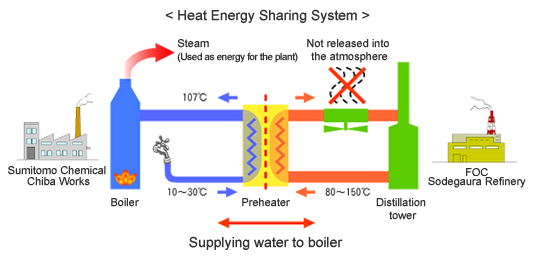
Low-grade Heat Power Generation System
The low-grade heat power generation system utilizes heat (low-temperature waste heat at temperatures up to 115ºC) recovered from the top of the FOC plant‘s distillation column to generate high-pressure ammonia which then powers the electric power generation turbine. The system has been in operation since October 2006.
The system employs a newly installed heat exchanger to recover waste heat, which would have been released into the atmosphere if a conventional air-cooled heat exchanger were employed. This reduces the use of fossil fuel that would normally be used to generate power.
The system offers superior operational reliability and is the world's first power generation system that uses a heat exchanger to directly recover low-temperature waste heat from a large-scale processing plant located in a petrochemical complex.
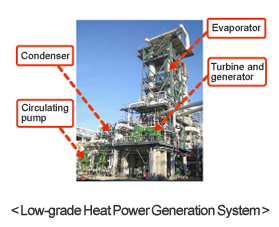
These systems alone enabled to cut the annual crude oil consumption by 10,700 kiloliter. Since neither the energy sharing system nor the low-grade heat power generation system use additional fuel, CO2 emissions are reduced by 28,000 tons. These systems are making a big difference when it comes to saving energy and saving the environment.